Process
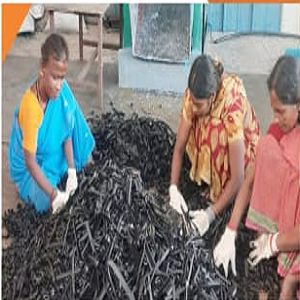
Segregation Process
The plastics that have to be shredded are sorted clearly, checked by the quality supervisor. Any quality issues found during the segregation is noted down immediately and actions are taken in order to maintain the quality. We do not Compromise in our quality. We have Employed technicians who know the differentiation of various typer in plastics.
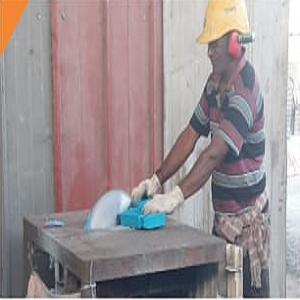
Cutting Process 1
(Smaller Articles)
In this process plastics are initially checked for any metal contaminations and if there is no such impurities present, we start to grind them into smaller pieces so that they may easily be recut without pressurizing the shreddeer. We take all safety measures with the cutting machine smaller is user to break the huge plastics inti smaller pressurizing the shredder. We take all safety measures with the cutting machine that is user to break the huge plastics inti smaller parts because it is really hard task employed there with huge risks.
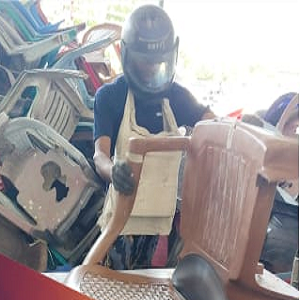
Cutting Process 2
(Bigger Articles)
As told above, the bigger and light articles are again processed into smaller parts for grinding. In this process we employ a heavier and bigger size machine along with a bigger blade so that the parts which are huge are cut down easily without any impact on the person doing this process. Most of the Bigger articles Like pallets, Car Dashboards, Cans, other huge Articles are processed in this machine.
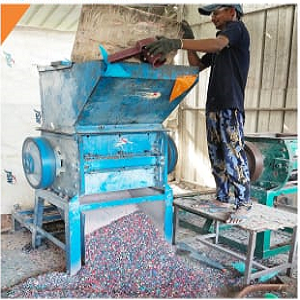
Shredding Process
This Has Been a Challenging task of all times. The Process of shredding plastics is a very complicated process since all plastics have various strengths. Once the process of shredding is complete, the material that is been broken into very small pieces are now ready for the process of washing.
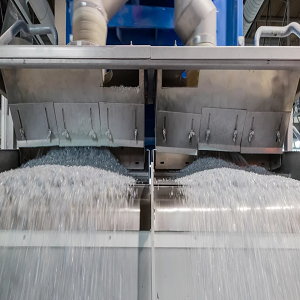
Washing Process
The Shredded plastic is then fed to the process of washing which rinses the plastic from impurities. The contaminated material settles down. Finally the dries plastic is ready for agglomeration process.
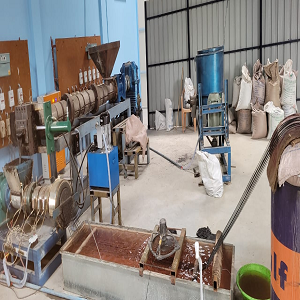
Extrusion process
The Process of melting up the plastics into raw material for making some useful product again is called the extrusion process. It comprises of a extruder which melts up the granulated form of plastics. It sends to the baby machine which in ture mixes up the melted plastic even more better and finally the granules are cut after they pass a water stream and packed in bags ready for the next process to get completed. Each Plastics Differ in their melting temperature which is handled by the operator of the machine.
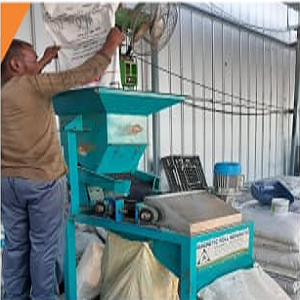
Magnetic process
in this process granules pass through a huge magnetic roller and the metal contaminations in the plastic granules are grasped. This process employs a technical supervisor who checks for the contaminated granules and separate them from the good material. The material is weighed again for the actual weight and packed in bags which in turn are ready for Despatch.
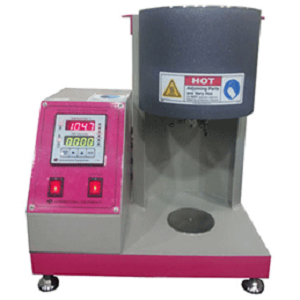
Melt Flow Index
In this process, we define the melt flow of the plastics that have been extruded, depending upon the customer needs. We compound the needed material and give melt flow as their specifications. There is a lab technician who checks the quality of the material every two hours to keep track of the specified melt flow.
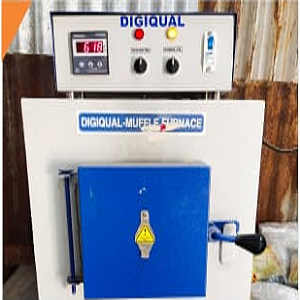
Ash Content
Granules are weighed using crucibles and kept in the furnace for about 20 minutes to get the actual test report of ash content present in the specified material.
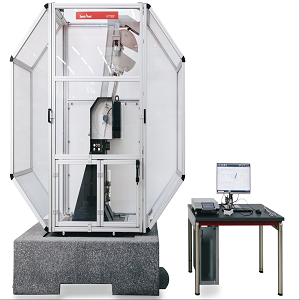
Impact Tester
The Granules are hand molded and the notch present in the molded plastic is placed on the impact tester and the pendulum is oscillated with the standard ASTM notified Device and the impact of the material is tested.